Search in Category
Filter Your Search

Shop by Category
PLCs
ET200PRO EM 4 DIO 4 DO DC 24V 05A
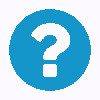
Don't see what you need?
Click here to let us know and we'll help you find what you're looking for.What is a PLC?
A programmable logic controller, or PLC, is a computer used for industrial automation that continuously monitors the state of integrated input devices and makes decisions based upon custom programs to control the state of output devices. These controllers can be used to automate processes, machine functions, or even an entire production line. PLCs are modular systems in that you can mix and match input and output devices to best suit your given application. The largest benefit in using a PLC is the ability to change and replicate a process or operation while vital information is collected and communicated.
How Does a PLC Operate?
A PLC receives information from connected sensors or input devices before processing the data and triggering outputs based on pre-programmed parameters. There are four basic steps in the operation of all programmable logic controllers; Input Scan, Program Scan, Output Scan, and Housekeeping. These steps take place in a repeating loop.
4 Steps in PLC Control Systems
- Input Scan
- State of all input devices connected are detected.
- Program Scan
- User created program logic is executed.
- Output Scan
- All output devices connected are energized or de-energized.
- Housekeeping
- Communications with programming terminals, internal diagnostics, etc…
Depending on the specific inputs and outputs, a PLC can monitor and record run-time data such as machine productivity or operating temperature, automatically start and stop processes, generate alarms if a machine malfunctions, and more. Programmable logic controllers are flexible and a robust control solution that is adaptable to almost any application.
What is Inside a PLC?
The Central Processing Unit, the CPU, contains an internal program that tells the PLC how to perform functions similar to the following:
- Control instructions located in the user’s programs are executed. This program is stored in “nonvolatile” memory, meaning that if power is removed, the program will not be lost.
- Communicate with other devices including I/O devices, programming devices, networks, and other PLCs.
- Communications, internal diagnostics, etc.
There are a few key features that set programmable logic controllers away from industrial PCs microcontrollers and other industrial control solutions.
- Input/Output (I/O): The CPU in the PLC stores and processes program data, but input and output modules connect the it to the rest of the machine. I/O modules are what provide information to the CPU and trigger specific results. These can either be analog or digital devices. Input devices may include sensors, switches, and meters while output devices might include relays, lights, valves, and drives. Devices can be mixed and matched for use with a PLC in order to get the correct configuration for their application.
- Human Machine Interface (HMI): A human machine interface (HMI) is needed in order to interact with a programmable logic controller in real time. These devices enable users to review and input information to the PLC through a simple display with a text-readout and keypad, or a large touchscreen panel that is more similar to consumer electronics.
- Communications: In addition to I/O devices, there may be use cases for a PLC to connect with other types of systems. Users might want to export data related to an application that was recorded by connected devices to a supervisory control and data acquisition (SCADA) system which has the ability to monitor multiple connected devices. All PLCs offer a range of ports and communication protocols to ensure that it can communicate with other systems.
What are Input/Output Devices?
Input and output devices are any hardware used by a human operator or other systems to communicate or interface with a computer. I/O devices, as the name implies, are capable of delivering data (output) to and receiving data from (input) a computer. Examples of such devices commonly used with a PLC are below:
Input | Output |
|
|
What to Consider when Choosing a PLC?
Every machine and industrial process that must operate in tandem with other components require precise controls that dictate how they operate. While PLC manufacturers can help you select the controller that will work best in your process, it pays to understand the variables that make specific programmable logic controllers best for particular operations. Below are some of the key factors to keep in mind when selecting a PLC:
- Power Supply: Will the system be powered by AC or DC voltage? Some PLCs can operate within a range of AC voltages and even on 24-volt direct current. One of the first decisions that need to be made, if your PLC will be powered by 120-volt or 240-volt AC. Most industrial application PLCs will accept either, but you will want to be sure. Most power supplies come embedded in the processor, where others are housed in a separate module outside of the PLC casing, or hardwired to the processor.
- Speed: Does the system run fast enough to meet my application’s requirements? Like personal computers, PLCs possess varying processing speeds based on their operating memories, microchip capacities, and other factors. How fast your PLC needs to operate will depend on the number, precision, and power required by downstream machinery and devices. Here are a couple of things to consider when deciding on the needed PLC speed for your application:
- Number of inputs and outputs the PLC will control
- Number of time-critical events in the process
- Operating time for component or process
- Preciseness of component response when triggered
- Total cycle time required to collect and process inputs and issue output instructions
- Type, format, and complexity of the program and instructions powering it
- Input/Output Capacity: Will the PLC be able to manage the number of inputs and outputs that my application requires? Processes require PLCs that can manage and integrate all the data input and instruction output sources included in the operation. Often, both input and output data arrive as digital and analog packages, so you will want a PLC that can accept and deliver along either path.
- Communication: How am I going to communicate with my Programmable Logic Controller? Many times, the appropriate instructions an industrial PLC needs to send are based on inputs received from the operator. The way those instructions are transmitted must be compatible with the PLC, whether they are sent via LED, toggle switches, pushbuttons, touchscreens, or other interfaces.
- System Footprint: Will the system be located in one place or spread out over a large area? The speed and distance to be covered can be largely determined by how widespread the control network is. If all the input generators and output targets are confined in a relatively small space, there may be more PLC options available. If, however, the signals must travel over a larger area, it may need to contain a remote as well as the local I/O functionality. Designing processes from scratch may allow plants to avoid this complication, but established facilities with components already in place may be forced to use PLCs that can manage where they sit.
How is a PLC Programmed?
Programming a PLC is usually done on a computer and is then downloaded onto the controller. Most programming software offers Ladder Logic, or “C”. Ladder logic is the traditional programming language, mimicking circuit diagrams with “rungs” of logic read left to right. Each rung represents a specific action controlled by the PLC, starting with an input or series of inputs (contacts) that result in an output (coil). Due to its visual nature, Ladder Logic can be easier to implement than many other programming languages.